BEC-Iowa Symposium 2023
- Published in News, Past Events
- Permalink
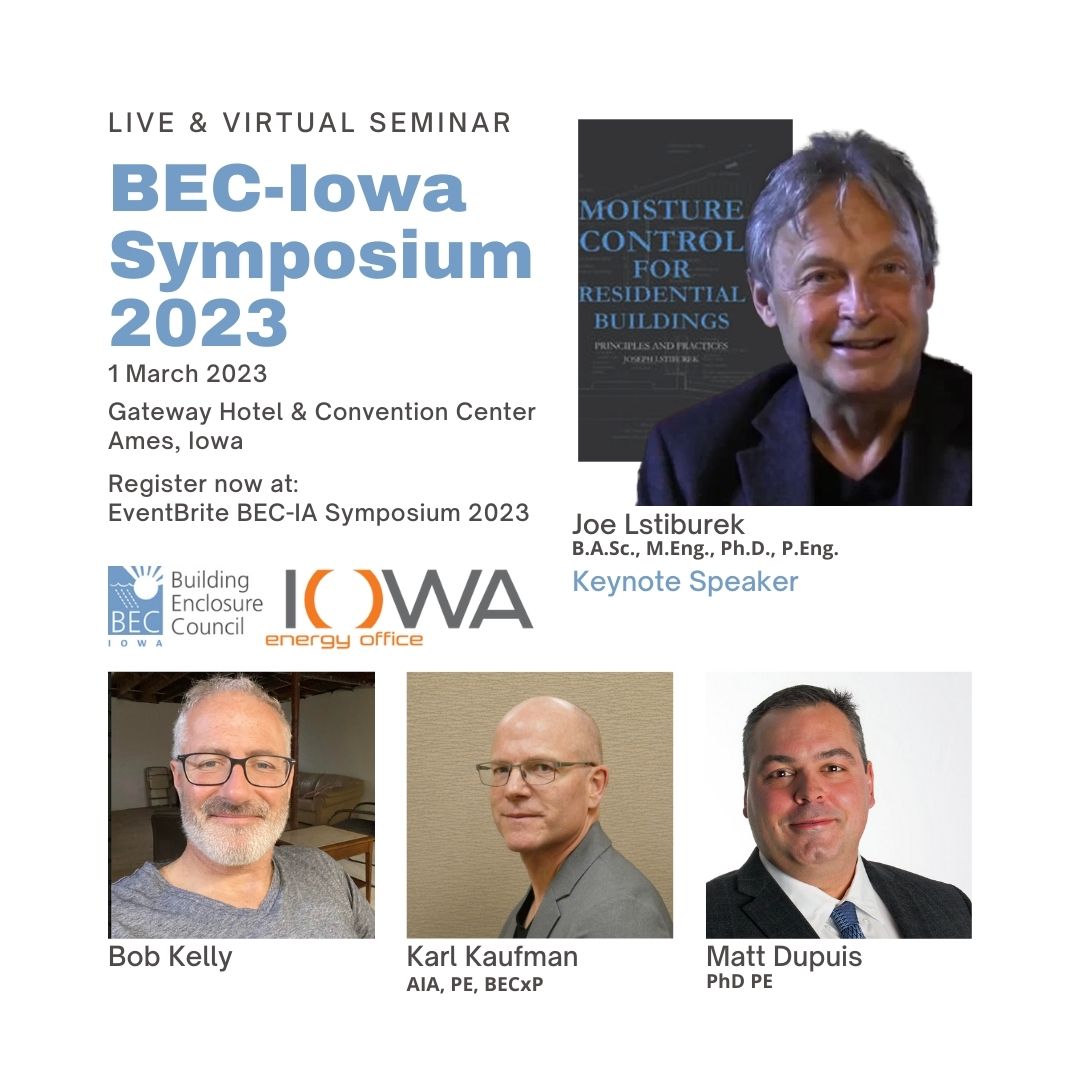
The Building Enclosure Council of Iowa, in collaboration with the Iowa Energy Center, is proud to present the 2023 BEC-Iowa Symposium. The Symposium includes a distinguished panel of speakers to discuss building science, with a focus on designing for cold climates. This will be a hybrid event with both Live and Virtual options available. Download a flyer for the event HERE.
Limited Registration
$80 BEC-Iowa Members
$100 General
Registration is required prior to the event. Ticket sales close February 21, 2023 at 11:59pm.
For in-person attendees, the event includes a continental breakfast and lunch.
For virtual attendees, the meeting link and information will be sent the week of the Symposium.
AGENDA
8:30am: Check-in, Sponsor Displays
9:15am: Opening Comments
9:30am: Presentation 1 – Joe Lstiburek
10:30am: Morning Break, Sponsor Displays & Announcements
10:45am: Presentation 2 – Bob Kelly
11:45pm: Lunch Break, Sponsor Displays & Announcements
1:00pm: Hands-On Exercise – Bob Kelly
1:45pm: Presentation 3 – Karl Kaufman
2:45pm: Afternoon Break, Sponsor Displays & Announcements
3:00pm: Presentation 4 – Matt Dupuis
4:00pm: Closing Remarks
SPEAKER INFORMATION
Dr. Joe Lstiburek, B.A.Sc., M.Eng., Ph.D., P.Eng., is the founding principal of Building Science Corporation and an ASHRAE Fellow. He is a building scientist who investigates building failures. Dr. Lstiburek received an undergraduate degree in Mechanical Engineering from the University of Toronto, a master’s degree in Civil Engineering from the University of Toronto and a doctorate in Building Science Engineering from the University of Toronto. He has been a licensed Professional Engineer since 1982.
The Wall Street Journal referred to him as “the dean of North American building science.” Fast Company magazine called him “the Sherlock Holmes of construction”. He is internationally recognized and his work has influenced building codes and standards in every climate zone.
He is a recipient of the Carl Cash Award from ASTM, a “Becky” from the Ontario Building Envelope Committee (OBEC) and the EEBA Legacy Award all for lifetime contributions to building science. He has also been inducted into the Building Performance Industry Hall of Fame and has received the NESEA Professional Leadership Award for “changing the way we think about building science and how we perform our work”.
Dr. Lstiburek is an acclaimed educator who has taught thousands of professionals over the past four decades and has written countless papers. He has a joy for telling tall tales to his proteges and audiences.
Presentation: There is No Such Thing as a Free Thermodynamic Lunch
Three big things have changed in our lifetime: we don’t build out of rocks and hundred-year-old trees anymore; we have very little energy exchange from the inside to the outside and vice versa; and we have heating, cooling, and ventilation systems that condition the inside almost year round. The newer materials are significantly more sensitive to water damage. The added thermal resistance has reduced drying potentials. Materials that get wet stay wet longer. Buildings are now mechanically ventilated. All of this has resulted in health and safety issues and durability issues. The only folks that are happy are the fire folks because the buildings are too wet to burn. So how do we fix this and still be energy efficient and use the newer materials? Manage heat, air and moisture differently. The physics have not changed, but the materials and our understanding has. This session provides recommendations on health, safety, durability and energy.
Learning Objectives:
- How changing energy flows have reduced drying potentials.
- How changing materials have reduced durability.
- How changing ventilation has increased problems rather than solving problems.
- How to build buildings that are safe, healthy, durable, comfortable and energy efficient.
Bob Kelly, is a 35-year veteran General Contractor, Master Carpenter, Inventor of WickRight, and a life-long student of Building Science. Everyday, he assesses moisture intrusion issues in masonry buildings in Chicago, pulling apart rotting roofs and walls, examining the sources of water damage and inventing practical solutions.
Around 2010, Kelly started receiving calls from owners of relatively new homes, experiencing water intrusion. He quickly recognized that the materials and construction practices used on most of these buildings were similar, as were the leak sources. He researched and met with masonry experts to understand how moisture moves through masonry, and observed first hand rotting trusses, the consequence of this pervasive problem.
Per Kelly, there were no products available on the market to prevent moisture intrusion AND dry out parapets – so he designed a solution.
Kelly’s clients were willing test subjects, having spent huge amounts of money with other contractors to fix their leaks with no positive results. After installing early versions of WickRight on a handful of buildings, Kelly observed the parapets and walls drying in the same manner – down to the foundation in some cases, or to the first through-wall flashing on most buildings. Based on his findings, he designed each WickRight vent to meet the needs of specific trouble areas on parapets, low-slope roofs and pitched roofs.
As a serial inventor, Kelly designs materials and tools not readily available, to repair his client’s buildings. Most notably, he designed a tent rafter system that attaches to parapet walls and keeps a roof dry in any kind of weather. He also designed a roof truss reinforcement bracket system that’s installed from the rooftop onto existing trusses.
Prior to founding WickRight, Kelly (Kelly Carpentry) worked mostly in Chicago’s North Shore communities, providing finish carpentry, renovation and general contracting.
Presentation: Saving Wet Masonry Buildings by Managing Bulk Water and Vapor at Parapets and Low-Slope Roofs
Masonry buildings constructed with CMU and embedded roof trusses are failing at an alarming rate in Chicago. An unfortunate combination of new materials and old-world construction methods, has led to this situation. Restoring these buildings requires a combination of bulk water and moisture vapor management. This course presents solutions that manage bulk water, dry out wet walls, manage condensation production behind roof membranes and, when caught in time, can prevent trusses from rotting.
Learning Objectives:
- Recognize signs of moisture intrusion and identify common moisture intrusion entry points.
- Describe how building science, supply chain and culture of the trades currently impact each other in the field.
- Identify contemporary basic low-slope roofing materials and common roof termination methods.
- Describe how condensation forms behind low-slope roofing membranes and in interstitial roof spaces.
- Describe how masonry and roofing materials and construction methods affect each other.
- Describe how providing pathways for moisture vapor to exit a building can restore a wet building to a healthy building.
- Explain how some compromised trusses can be reinforced to restore structural integrity.
Hands-On Exercise: Installing Vented Flashing on Parapets and Low-Slope Roofs to Manage Bulk Water and Vapor
This course is a hands-on demonstration of how to plan for flashing installations in common trouble areas on masonry buildings, including: parapets, perimeters of low-slope roofs, window and door openings, and under window and door sills. This course will demonstrate how sheet metal flashings, as well as flashings made from self-adhered materials, help manage bulk water and how vented flashings allow moisture vapor to exit buildings to dry out and keep masonry walls dry, as well as manage condensation production behind roof membranes. (JOIN IN-PERSON FOR THE FULL EXPERIENCE!)
Learning Objectives:
- Identify sheet metal and self-adhered flashing types and common parapet finishes.
- Describe how flashings divert bulk water away from building materials/construction transitions.
- Explain how vented flashings exhaust moisture vapor and heat, and how this prevents condensation from forming behind low-slope roofing membranes and in interstitial roof spaces.
- Explain how Door and Window Pan Flashings prevent water from damaging door and window openings and adjacent flooring and window components and walls.
- Explain how to make End Dams from Self-Adhered flashing and how these flashings prevent water damage in Door and Window openings.
- Describe how to install door and window sill flashings.
- Explain how to determine if a truss can be saved or needs to be replaced, and describe how the featured truss reinforcement brackets are installed.
Karl Kaufman, AIA, PE, BECxP, is a Building Enclosure Commissioning Provider at SystemWorks. Karl’s interest in building enclosures grows from the belief that we can collectively improve the building’s overall performance and sustainability by focusing on the design and construction of the enclosure. While a licensed architect and engineer, he focuses on QA & QC during the design and construction phases as a BECxP, CxA+BE, and ABAA Licensed Field Auditor. In addition to stand alone diagnostic investigations, this has given him the opportunity to analyze, understand, and test a variety of constructed assemblies.
Presentation: Cold Weather, Codes, and Condensation
Heat and moisture in building enclosures are inextricably linked despite provisions regulating their control being separated across 2 different codes. Compliance with these provisions does not guarantee an assembly free of condensation or mold growth. The thermal efficiency of the enclosure and the potential for moisture problems are impacted by the insulation strategy. The dynamic properties of typical construction materials, their ability to throttle moisture and heat, and how their strategic incorporation can be used to improve the hygrothermal performance of the wall assemblies will be examines, particularly as they relate to split insulation strategies in cold climates.
Learning Objectives:
- Identify risks associated with prescriptive IECC provisions for insulation and IBC vapor retarder options.
- Understand alternative paths to meeting the opaque exterior wall requirements of IECC and IBC.
- Understand the criteria for acceptable wall performance in general, and how they specifically relate to hygrothermal conditions that impact indoor air quality and durability.
- Recognize how the material properties and location of components affect the wall’s hygrothermal performance.
Matt Dupuis, PhD, P.E., is a Principal at SRI Consultants Inc. Dr. Dupuis is a licensed Professional Engineer with almost 25 years of experience. His area of specialization lies within moisture movement, temperature modeling, solar reflectivity, research, and failure analysis. He has worked in the United States and internationally. His experience also includes waterproofing and steep roof assemblies. He routinely lectures at the University of Wisconsin-Madison.
Presentation: RoofTop Failures – Learning From Mistakes to Prevent in the Future
This session covers the past several years of rooftop failures, from a technical perspective. Topics covered include common low slope design, installation and maintenance mistakes that happen on roofs, and why. Potential solutions are offered to prevent these issues at a design phase, or during the roof service life. Geared for Roofing Contractors, Designers, Code Officials and more, learn what mistakes are costing money on low slope roof installations and how to prevent them.
Learning Objectives:
- The differences and proper installation of low-rise foam adhesive with fully adhered roofing systems.
- Understanding concrete roof decks and moisture including issues with light weight concrete release of water during curing process.
- Understanding cold roof decks and moisture including issues due to mechanical duct penetrations.
- Understanding cold storage roofs and issues with moisture condensation.
- Understanding roof performance issues due to cost implications.
CLICK HERE to register
This event has been approved for AIA continuing education credits. Attendees will earn up to 4.5 LU/HSW.
Please submit your AIA number during your Eventbrite Registration or email contact@bec-iowa.org.
Interested in becoming a sponsor for this event? Choose one of two options:
- Complete the Symposium Sponsorship Form and mail it with your payment.
- Complete the Symposium Sponsorship Form and email it to contact@bec-iowa.org. Submit payment online by clicking on the sponsorship icons below:
Questions? Please email us at contact@bec-iowa.org.